Germany’s ThyssenKrupp Marine Systems (TKMS) can provide a practical endorsement of its bid to supply Australia’s Future Submarine - a state-of-the-art shipyard with six submarines under construction, three more undergoing refit or maintenance, and ongoing research and development activity.
Julian Kerr | Kiel, Hamburg and Berlin
In its own way, this sprawling Kiel facility epitomises what TKMS says it’s offering the Sea 1000 program - efficiency, experience, and a design capability honed to meet the varying and often unique requirements of disparate and demanding international customers.
Since 1960 TKMS via its subsidiary HDW has delivered 161 diesel-electric submarines to 20 navies. Of this total, 123 have been built for international customers including six NATO navies, 51 of them in the customer’s country. Other significant customers include Israel, South Korea and Singapore, with future regional sales prospects in India and Thailand.
In the process of winning 60 per cent market share, TKMS has developed what it says is the world’s largest industrial support base for conventional submarines, a capability doubtless assisted by the presence in more than 80 countries, including Australia, of its parent company, engineering giant ThyssenKrupp.
"All TKMS contracts are fixed price 'and we have a good track record, otherwise we’d be broke'."
Although SEA 1000 is currently the primary focus of TKMS Australia, the company is also bidding the 38 metre fast patrol boat of its Blohm and Voss subsidiary for the Pacific patrol boat requirement, and in due course will be competing for the SEA 5000 Future Frigate contract with its sophisticated Blohm and Voss MEKO A-400 RAN.
Defence Minister Kevin Andrews accompanied by Head of Submarine Capability Rear Admiral Greg Sammut RAN toured the Kiel facility in April. Here they would doubtless have been gently reminded of the on-budget, on-schedule construction in Australia of the Blohm and Voss-designed ANZAC class frigates.
As subsequently pointed out by TKMS executives, the transfer of intellectual property (IP) in that program was such that Blohm and Voss involvement was not required in the frigates’ complex anti-ship missile defence (ASMD) upgrade.
Construction underway during the Minister and RADM Sammut’s tour ranged from the welding of sections of pressure hulls in various stages of completion to advanced work on a German Navy Type 212 Batch 2 and a 2,300 tonne Israeli Dolphin II - probably the company’s most capable platform to date.
What the Minister and RADM Sammut would not have seen were the more than 800 submarine design specialists whose workflow, now including the completion by November of a concept design for the Sea 1000 competitive evaluation process, produces a new design or an evolution of an existing type, every five years.
Notwithstanding the company’s experience, TKMS has yet to construct a submarine in the 4,000 tonne range; generally regarded as the size required to meet Australia’s requirements. This is not regarded as a problem by TKMS, whose designs have steadily grown in size and capability to meet customers’ specifications.
Philip Stanford, CEO of TKMS Australia and a former Collins class commanding officer, describes the Type 216 as a reference design on which work began in 2008.
“As a reference design it represents a compilation of what we see as the latest technology applicable to a 4,000 tonne submarine,” he says.
“There is a managed risk in a new design; there’s no such thing as a MOTS (Military Off The Shelf) submarine, but more than 80 per cent of the TKMS Future Submarine design/detail/equipment is already integrated and at sea.”
The balance involves lithium ion batteries, a methanol reformer for an enhanced Air Independent Propulsion (AIP) system, and a larger version of the Siemens Permasyn alternating current permanent magnetic motor that already propels the submarines of seven navies. This upgrade will increase output by 50 per cent over the 2.85 megawatt Permasyn motor powering the 1,860 tonne HDW Type 214.
According to Siemens, maintenance is invariably confined to changing the lubricating oil of the two motor bearings, and occasional cleaning of the heat exchangers.
Diesel engines, the cause of much angst in the Collins class, will be four MTU 12V Series 4000, the commercial variant of which is already available in Australia. These are derived from the MTU 396 whose legendary reliability saw the designers of the Type 212 feel able to rely on a single such engine.
Predicated on a 4,350 tonne (submerged displacement) platform but designed to be scaled up or down, the Type 216 features double hulls, two decks, 80-day endurance, a low indiscretion rate and a 60-strong crew, with limited additional accommodation for special forces or sea-riders such as specialists and trainees.
Cruising range under conventional diesel-electric power is put at 10,400 nautical miles at 10 knots, with an additional 2,600 nautical miles at four knots utilising AIP. In addition to its six torpedo tubes, the Type 216 also features an innovative vertical multi-purpose lock just aft of the sail for cruise missiles, unmanned systems or divers.
Scaling-up a pressure hull by the same quantum as 2,400 tonne to 4,000 tonne has been undertaken many times, TKMS says. This entails the same hull material, the same calculation systematics and tools for submarine engineering, the same stealth calculations and design, the same underlying layout parameters, and the same degree of quality assurance and documentation.
Design risk
The design risk therefore is in the integration of the systems and subsystems, most of which are already at sea in the Type 214, the company comments. Those that are not, include the AN/BYG-1 (V) combat management system (CMS) and the Mk48 Mod 7 CBASS (common broadband advanced sonar system) heavyweight torpedo that now equip the Collins fleet.
Both systems continue to be jointly developed and exclusively fielded by the US Navy and Australia, and both are mandated for the Future Submarine. It’s here that TKMS emphasises that no one country’s submarine is the same as another’s, even if they’re nominally the same class. The clear implication is that capabilities within a given class can therefore differ widely according to the requirements, the skills and presumably the pockets of the operators.
So too the fitouts, with TKMS pointing to extensive experience in integrating a variety of combinations of systems, including different CMS and weapons.
As examples, TKMS refers to Type 212 Batch One submarines for Germany and Italy that were equipped with a Kongsberg CMS, whereas the Type 212 Batch Two for Germany has reverted to a CMS from Atlas Elektronik (51 per cent owned by TKMS).
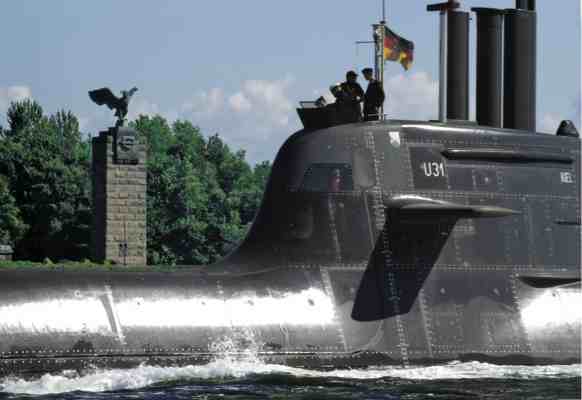
Similarly, customisation of two Type 218SG submarines recently ordered by Singapore, believed to be evolutions of the TKMS Type 209, reportedly includes an Atlas Elektronik CMS that is being further developed by Singapore-based ST Electronics and will be supplied by the customer.
And it was after close engagement with the Israeli navy on a variety of systems that saw the 2,300 tonne Dolphin class - reportedly nuclear-armed –“emerging as a unique submarine for Israel that precisely meets their needs”, TKMS notes.
Technically, integrating the AN/BYG-1 (V) and the Mk 48 Mod 7 in a Type 216 is not an issue and the handling of sensitive information is a normal process, says Stanford.
“Early discussions with US companies lead us to the conclusion that this can be dealt with in a way that is acceptable to the Commonwealth and USN,” Stanford said.
Also based on past experience, TKMS is equally confident about the viability of the options it is advancing in the comparative evaluation process for construction of the Collins replacement either in Australia, in Germany, or a combination of the two.
“We’ve supported the construction of our designs in South Korea, Turkey, Greece and Brazil in addition to Germany and we’re more than happy to build in Australia with a full transfer of Intellectual property,” Stanford said. “This comes down to discussions with Government. We’ve developed a process of auditing a customer’s shipyard and then developing a suitable program to upgrade and enhance the capabilities to the standard required to deliver the submarines,” he explained.
“We’re ready to talk with the government and Defence to ensure that the appropriate infrastructure is available with the correct production processes, with the correct management, to ensure an efficient build.”
The so-called hybrid option is up to TKMS to define, Stanford explains.
“It could involve some sections being built in Germany, skills training, and the whole boat being assembled in Australia; it could involve a ‘material package’ concept where materials for the boat would be delivered from Germany to ensure quality control and reduce program risk.”
Torsten Konker, a member of the TKMS Executive Board, told ADM in Kiel in mid-May that the company would consider a bid for ASC if the German company was selected as the preferred tenderer for Sea 1000.
“We’re ready to talk with the government and Defence to ensure that the appropriate infrastructure is available with the correct production processes, with the correct management, to ensure an efficient build.”
Rather than simply entering a supply contract with an Australian shipyard, TKMS would consider its acquisition as part of the company’s overall responsibility for the success of the program, and of its interest in playing a long-term strategic role in Australia.
Speaking separately in Hamburg, TKMS Australia’s chairman Dr John White said the company had put out some key messages that TKMS was committed to replicating its German naval construction capability as needed in Australia.
Dr White, head of Anzac frigate construction and co-author with former US Navy Secretary Donald Winter of last year’s government-initiated Winter/White review of the troubled AWD program, said this would be done through the facilities and capabilities that were already in place in Australia, upgraded as needed.
“That certainly includes ASC should it be available for privatisation,” he stated.
While TKMS executives studiously avoided any criticism of their Sea 1000 competitors DCNS of France and Soryu class constructors Mitsubishi Heavy Industries and Kawasaki Shipbuilding Corporation, they did occasionally refer in the abstract to the importance and difficulty of technology transfer, whether for construction or sustainment.
They also stressed the benefits to be derived from lithium ion batteries, albeit as a supplementary energy source to AIP rather than in its place. The attributes of the TKMS/HDW AIP system were conclusively established in 2013 when a German Navy Type 212 on its way to exercises in the US established a new record for non-nuclear submarines of 19 days eight hours in submerged transit without snorkelling.
Although Collins class boats undertake lengthy submerged transits on their way to operational areas, their endurance without snorkelling is understood to be about three days.
TKMS maintains its system is superior to any other AIP system by a factor of at least two.
For 100 kWh of energy stored as fuel and deducting all energy losses, including cooling, 60 kWh net are available for submarine propulsion and consumers. While this and other such performance claims may be contested, what was noticeable in visits by a small group of Australian journalists to TKMS facilities in Kiel and Hamburg was a refreshing readiness at senior level to respond to rather than evade questions, however pointed.
Konker emphasised that all TKMS contracts, whether for submarines or for surface ships, were fixed price “and we have a good track record, otherwise we’d be broke”.
Although Sea 1000 numbers (current speculation is eight or nine hulls for the life of the program) and build schedule have yet to be made public, Konker said he stood by the company’s statement last year that it could deliver 12 Type 216-type submarines for Australia for $20 billion.
The first of these could be delivered within 10 years of inking a contract encompassing detailed design and construction, thus avoiding the need for expensive extensions to the service life of at least some of the six-strong Collins fleet.
The German government was ready to provide cost analysis of any TKMS proposal and, if necessary, to advance it on a government-to-government basis, Konker said.
This backing was reinforced in a meeting with federal parliamentarians headed by Uwe Beckmeyer, State Secretary of the Ministry of Economics and Energy, who toured ASC in early April with other German politicians, defence officials and industry representatives, and spoke to potential suppliers.
Although not as part of the formal meeting, one parliamentarian disclosed to ADM that a possible visit to the US by an official delegation was under consideration to ensure that Japan’s Sea 1000 bid was not the recipient of “unfair” US support.
Disclaimer: Julian Kerr travelled to Germany
as the guest of Thyssen-Krupp Marine Systems.