Navy’s Hunter frigate program has been in the news of late, particularly with regard to construction delays and growth margin concerns. ADM Senior Correspondent Julian Kerr recently spoke with Managing Director of BAE Systems Maritime Australia Craig Lockhart to find out more.
Although the start of construction of the first Hunter-class frigate has been delayed for up to 18 months, the head of the build team that will deliver nine of the Future Frigates to the Royal Australian Navy (RAN) is confident that progress with shipyard facilities, prototyping procedures and design augurs well for the future.
With more than 30 years industry experience and leadership in the civil nuclear, submarine and surface ship sectors, Craig Lockhart is well placed to update on progress towards the construction phase of the $45 billion Sea 5000 project.
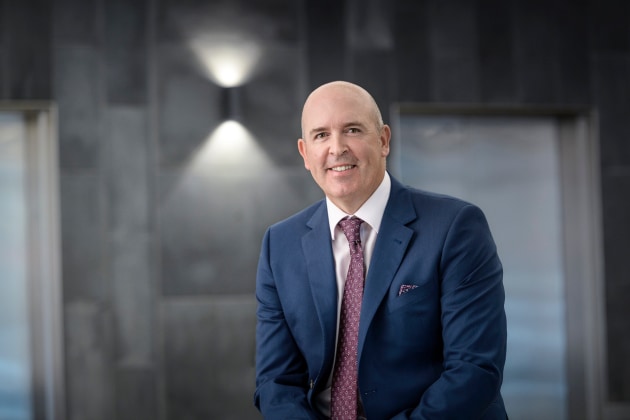
Particularly so, given a previous role as Managing Director of Babcock International’s Naval Marine in the UK involved more than 6,000 staff across two naval dockyards, two naval bases, two shipbuilding yards and various technology and engineering centres.
ADM: What is the current status of the Osborne Naval Shipyard?
Lockhart: It’s settling down very well. We gained access late last year, five months later than expected because of the COVID-induced late arrival of equipment from Europe, but that time has already been largely recovered. We cut first steel in December for the prototyping phase that is testing systems, processes, facilities, and the competencies of a workforce now approaching the 1,300 mark. While we had no input to the design of the yard, we are now accommodating that generic design within our own strategy for a highly productive advanced digital shipyard. As the operator of the yard, we’re maximising our ability to build good ships through our production line process. In terms of the primary manufacturing elements, that’s all complete. We’re working now to implement a digital environment. Most of our workers will access work orders, risk assessments, critical design information and safety instructions through handhelds and tablets.
The Steel Fabrication and Unit Assembly Hall at Osborne – Building 20 – is where we’re starting to build the prototyping blocks, starting with units. The first unit of the first block 16 is currently making its way down what we call the pulse line stations. Each station adds complexity to what was initially flat steel plate as this is moved up the shop floor on jig wagons – first assembly, then structures, then robotics delivering high quality welds with zero defects, then the creation of block units. The focus has been on doing it safely, doing it well, and then concentrating on doing it efficiently, so we’re now measuring productivity as we move from station to station every four weeks. We keep the same teams on the same stations, it’s far easier for us to measure the effectiveness of that sort of process flow.
Furthermore, we’ve established a research and technology function at Tonsley Park in Adelaide at Flinders University’s Line Zero Factory of the Future facility. It’s not in the shipyard because it’s really a sand pit where we can work with SMEs, academia and Defence scientists to fully explore, test, rationalise and consolidate future technologies that we might want to bring in as part of our connected worker, connected yard, connected supply chain and connected ship ethos.
ADM: What was behind the June announcement on the delay to the start of Future Frigate construction?
Lockhart: We’d had discussions with the Commonwealth about the design effort and the Systems Definition Review (SDR), a major milestone that establishes the functional baseline of the ship. SDR commenced in March and it’s scheduled to be completed in November, allowing work to move on from functional baseline to system and detailed design. Through the SDR we assess design maturity against the capability and whole of ship performance requirements, including the integration of the Australian Government mandated changes such as combat systems. One of the complexities was the maturity of the First of Class design as we moved towards manufacture, particularly as we also unpacked the Australian combat system, including the radar. The impact of the UK COVID-19 situation on the Type 26 program in the UK has also created significant challenges. It ultimately meant we would be forced into a sub-optimal build process.
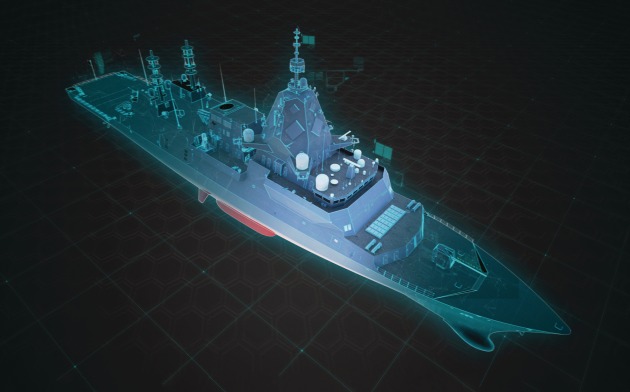
We normally build a naval ship in a number of blocks starting at the bottom in the middle and then working aft, then to the fore end and back up through the middle of the ship to the mast. Some of these blocks are in design zones that have been heavily impacted by the extent of significant combat system changes but nothing outside a normal First of Class program. The impact of the UK COVID-19 situation on the sister Type 26 program in the UK has also created challenges. A shift of the cut steel date will allow us to achieve the optimal design maturity in those high-change design zones of the ship, to ensure we can build the ship efficiently and effectively, reducing program risk. This gives us a much higher level of certainty on the delivery of the ships and more potential to compress the schedule over Batch One. A way of thinking about it is “going a bit slower to go fast”.
We’re still getting supplier information day by day, week by week, on the Australian-mandated changes and that informs where we exit SDR and what level of maturity we take in the design.
ADM: Was the delay option driven by the UK or by Australia, or has the complexity of the program simply been underestimated?
Lockhart: We’ve been pretty honest about the challenges in terms of maintaining ship margins and weight, as we’ve sought to understand the key changes. Some equipment on the UK’s first-of-class HMS Glasgow was heavier than predicted and that weight and complexity carries through to the reference ship design. Likewise, we’re having to take into account the Aegis combat management system, the CEAFAR 2 phased array radar and other Australian Government mandated changes. It’s a mixture of things and my job is to ensure we end up with a design that still meets the key performance criteria whilst giving the RAN the capability they need.
ADM: How significant are the design changes required for the Australian-mandated equipment?
Lockhart: CEAFAR 2 is a hugely capable radar but with that comes challenges; it is a very power-consumptive radar. So, the power dynamics onboard the ship are much more complex than its direct peers. The radar is heavier than the UK equivalent and when we put weight up high, it has a corresponding effect on ballast and seakeeping. But these are challenges that are common with first-of-class design and builds which we’d normally see anyway.
ADM: There’s concern about a growth margin of only 3.3 per cent of the light-ship weight of the Hunter, reportedly 8,200 tonnes, and a full displacement weight of 10,000 tonnes which is 1,200 tonnes heavier than the UK reference design?
Lockhart: We’re providing a Light Ship weight baseline ship that has been designed to meet our customer’s key performance criteria. Once we’ve got through SDR we can predict within the design and build models with a level of through-life growth margin. Final displacement is a matter for the RAN – how many missiles they take, how much fuel is on board, how many toolkits on the deck. Ultimately the decision on future through life upgrade/improvements by the Navy drives the need for a margin consideration, throughout the design and build process we also have margins that we consume as part of this process, all of which is carefully managed against those future growth expectations.
ADM: What changes are being made to the Hunter-class hull?
Lockhart: We’re making the ship slightly fatter over the majority of its (149.9 m) length. We’re not changing any of the ship systems, we’re just providing more buoyancy and stability and margins which the RAN can use in the future.
ADM: Design separation is the other major milestone scheduled for this year, transferring the Type 26 control processes, tools and systems from the UK to Australia. How will this be done?
Lockhart: A lot of the information originates in the reference ship design and therefore is governed to UK export standards. So, we have to make sure we’ve got information management protocols and processes in place, first and foremost. And then we are able to put in a clear demand statement – what information do we need in support of work, why and by when?
And now we’re doing that zone by zone. We’ve been building and testing the data repository through our tool that allows us to transfer and manage 10,000 artefacts per week – design information, drawings, data, videos, diagrams – and the tool has performed exceptionally well. We’re taking a cut of the reference ship model, we’re separating it in the CAD model, and we’re transferring it to Australia for us to manage that detailed configuration as we go through detailed design. But there will still be core and common elements between the Hunter-class project, the UK’s Type 26 and Canada’s Canadian Surface Combatant (CSC). And we still have a process by which major change that is offered up to any one nation or one class is also offered up to the other two nations and classes. Each nation can potentially benefit from changes that others are considering.
ADM: How complete will the reference ship design be when you receive it?
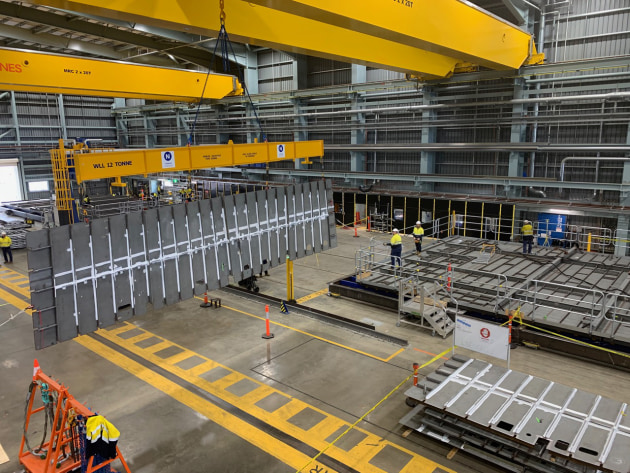
Lockhart: There will still be changes because HMS Glasgow has yet to be launched and fully outfitted. But we receive weekly and monthly metrics, we have daily calls with the UK, we have people embedded in the UK program who are able to attest to the UK’s performance against its own program. They’ve been working hard to deliver finalised compartments to the Navy and that requires them to have absolute accuracy in their data environment. And we benefit from that. A lot of our detailed design will be done in Melbourne, complementing what we deliver at Osborne.
ADM: Could the design be changed to increase firepower?
Lockhart: We will provide the Commonwealth with an understanding of the capability margins that could be within the ship. We will provide all of that analysis within the current SDR outcomes, and that really informs the Commonwealth’s and the Navy’s ability to decide what they want on Ship One Batch One; Batch 2 and Batch 3 before we go into manufacture contract.
ADM: What is the contractual situation?
Lockhart: We’re currently under a Design and Productionisation (D&P) contract that’s governed by the Hunter Head Contract signed in December 2018. It involves us building up capability in the yard, progressing detailed design from the reference ship, delivering long lead items into the supply chain, and AIC requirements. We’ll eventually move from D&P into a Batch One contracting environment prior to the start of construction. We’re now working closely with our customer to determine the requirements for Batch One and the next contracting phase.
ADM: You’ve expressed concerns about future skills shortages. Has anything changed?
Lockhart: We’re all fishing in the same pool for those critical engineering, systems engineering, design and capable supply chain knowledge resources.
Without a national response to generating more numbers in the hopper, our challenge is not going to diminish in the next 10 years. Systems engineers, everything from combat, to ship, to platform, to surveillance, post-graduation really face a decades-long experience journey. Unless we align ourselves nationally with academia, with the Department of Trade and Industry and stay focused on the workforce challenge, these pools of people are not going be available when we need them most.
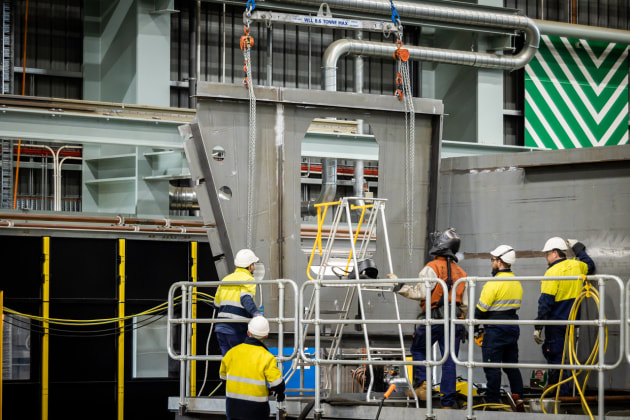
ADM: How are things travelling with Saab and Lockheed Martin in the combat system integration area?
Lockhart: We’ve come through a very intensive design period and the ability of our three organisations to work together is paramount to the success of this project. We put a lot of effort into the relationship, I speak to my fellow CEOs on a weekly basis, we have active working groups and a lot of cross-fertilisation, and the team is working very well together.
ADM: Rating the program as it stands from 1 to 10, how would you mark it?
Lockhart: It’s under good control. The program challenges are understood and being worked through. We know what the risks are; these are well-verbalised and communicated very clearly to government, Navy and CASG. Does that mean that the challenges are any less significant in producing a first-of-class in the UK and then first-of-class in Australia and then a first-of-class in Canada? No, it doesn’t mean that. So, you know, I’m never going to rate myself anything better than a five out of 10. We can always do better.