Industry conversations about Sea 5000 are at fever pitch, with a down-selection imminent. However, the majority of dialogue seems to be centred on Australian Industry Capability (AIC) and the program’s role in the National Shipbuilding Strategy. Anti-Submarine Warfare (ASW) capability, which is the primary strategic purpose for the Future Frigate acquisition, has received far less attention.
With this in mind, this article seeks to provide a comparison of the reference ASW configurations and viable upgrades for the three competing vessels, based on publically available information. To recap, the contenders include the F-5000 from Navantia (referenced from the Hobart Class DDG), the Global Combat Ship Australia from BAE Systems (referenced from the Royal Navy’s Type 26) and the FREMM-A from Fincantieri (referenced from the Italian Bergamini Class FREMM).
Importantly, when the Future Frigates enter service, from around 2030, the Hobart-Class DDG – which currently has the Navy’s most advanced ASW capability – will have been in service for over a decade and be well down its own upgrade path. The systems performance and operational effectiveness of the Future Frigate will inevitably be compared to the RAN’s lived experience with the DDG’s capability, especially as the ships will share the same highly trained Navy personnel. For this reason, this article baselines the Sea 5000 contenders’ ASW configurations against the DDG’s known system attributes.
Equally importantly, overall fit for purpose is not just based on sensor system characteristics. In building an overall ASW capability though the DDG and Future Frigate programs, the RAN’s ASW effectiveness will be highly reliant on the ability to cross-train and cross-operate using common user interfaces, and on expertise in operating towed sonar elements in difficult sea states or while manoeuvring (with number and type of required towed elements being a major determinant of deployment difficulty). It will also increasingly rely on the extent to which the ASW system can provide one integrated ASW picture to the command system from its sensors and – as the RAN moves towards multi-statics (see box for more on this) – from remote elements such as sonobuoys, helicopters and unmanned vehicles.
F-5000
As Navantia’s overall offer is based on maximised commonality and continuity with the DDG, the F-5000 offers the clearest reference configuration and roadmap. The F-5000 is expected to replicate the DDG’s Ultra Integrated Sonar System (ISS), consisting of the Ultra ISS Hull Mounted Sonar (HMS) and Ultra’s single horizontal Variable Depth Sonar (VDS) array, which contains both active and passive elements in the same array. The incumbent torpedo defence system is the SLQ-25 Nixie, operating as a decoy in conjunction with the torpedo detection capability within the VDS.
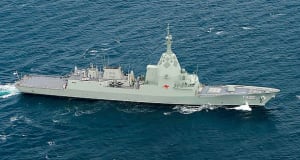
Stern impacts of ASW systems on the reference F-5000 are the same as the DDG; one ISS VDS winch and one SLQ-25 Nixie winch make up the majority of the platform size, weight and power (SWaP) allocation. In terms of operations, two towed elements are required to be in the water for full ASW functionality.
Due to the architecture of Ultra’s ISS, the F-5000 is expected to carry forward Ultra’s integrated processing layer which offers full bi-static capability and full commonality of operator interfaces. The F-5000 will naturally benefit from the DDG’s capability upgrade path, including the work to be undertaken through Sea 4000 Phase 6.
Two potential near-term modifications to the F-5000 reference configuration seem worthy of consideration by Navantia. The first is the substitution of the existing Ultra HMS for Ultra’s S2150 HMS (which is the reference ship HMS on the BAE GCS-A), a system of similar outboard size but with higher capability, and which offers inboard SWaP savings.
The second is the integration of torpedo defence capability into the Ultra ISS single horizontal VDS array. This is known to have been an option in Ultra’s Sea 4000 offering, and it would provide the significant SWaP saving of removing the need for a separate SLQ-25 Nixie winch and array. This space could be reserved for potential future ASW capability; including the evolved VDS configuration discussed later in this article. It would also mean that from an operational standpoint, one single towed element containing VDS and torpedo defence capability would provide the F-5000’s full ASW functionality.
GCS-A
The BAE’s GCS-A reference ship contains the Ultra S2150 HMS, and a Thales 2087 VDS (a UK version of the CAPTAS 4 system). The 2087 VDS and CAPTAS 4 are traditional VDS designs which have two separate towed elements - an active hard body transmitter and a passive receive array. The incumbent torpedo defence system is Ultra’s S2170 Surface Ship Torpedo Defence (SSTD) system rather than SLQ-25 Nixie.
Size and weight of ASW systems on the GCS-A stern are significantly higher than the DDG, although the vessel has been designed from the outset to accommodate this impact, so it does not represent design modification risk. Two Thales 2087 VDS winches, one VDS hard body over-boarding system, and one Ultra S2170 SSTD winch make up the majority of the SWaP allocation, and in terms of operations, all three towed elements are required to be in the water for full ASW functionality.
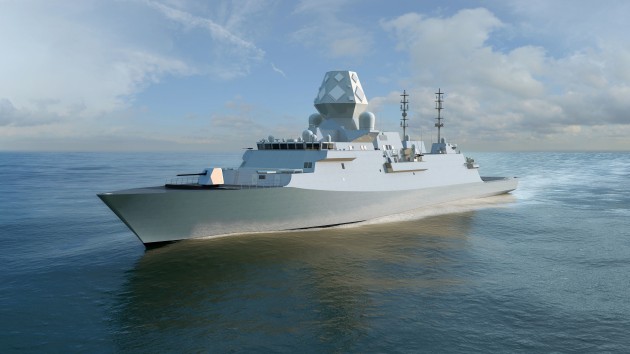
From an ASW system architecture and integration perspective, the GCS-A is unique as it is the only of the three competing platforms that has both Ultra and Thales systems in its reference design. As a result, the reference configuration does not have an integrated ASW approach nor inherent bi-static capability, and what sensor data fusion occurs is achieved in the Command Management System (CMS).
Similarly, the GCS-A’s reference vessel does not come with an operator interface providing a unified ASW picture, and its displays are unlikely to offer commonality with DDG user interfaces. This is a reflection that the vessel was designed to meet UK Royal Navy requirements, where the HMS and VDS sensors are used for independent tasks.
The most obvious near-term upgrade to the GCS-A reference configuration is to address processing integration and interface commonality to bring it closer to Australia’s capability development path commenced with DDG. Ultra’s S2150 HMS, already on board the GCS-A, provides a low-risk path as its software is known to contain the ISS integrated processing layer (which would provide bi-static capability if Thales 2087 VDS data could be brought into the system) as well as ISS-derived user interfaces. Thales is also considering integration issues through a developmental proposal called BlueScan.
FREMM-A
The FREMM has an established ASW system baseline consisting of the Thales 4110 HMS and the Thales CAPTAS 4 VDS (again a traditional VDS with separate active and passive towed elements). The FREMM also employs the SLQ-25 Nixie for torpedo defence.
Size and weight of ASW systems on the FREMM reference design are significantly higher than the DDG, although like the GCS-A the vessel is designed and built to accommodate this impact. Two Thales CAPTAS 4 VDS winches, one VDS hard body over-boarding system, and one SLQ-25 Nixie winch make up the majority of the SWaP allocation. In terms of operations, all three towed elements are required to be in the water for full ASW functionality.
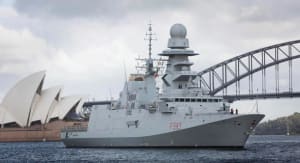
While all major ASW elements are provided by Thales, the FREMM is not known to have existing bi-static capability, with sensor data fusion and presentation to operators being achieved in the CMS. Again this is based on the ASW requirements of the FREMM’s European parent Navies.
Like for the GCS-A, the lack of inherent ASW integration of the FREMM provides the highest near-term opportunity for beneficial ASW system modification. Given the incumbency of Thales sensors, Thales’ developmental BlueScan architecture is the most likely route to providing the FREMM with a bi-static capability as well as enhanced user interfaces. However, organic commonality with the DDG’s displays and systems is not in play.
Evolved VDS options
In assuming a ship build schedule split into three flights of vessels, the Sea 5000 build program allows for the introduction of more significant capability steps as the program progresses. Thales and Ultra have both indicated capability options, especially in VDS systems evolution where both capability and platform impact is high, that might be relevant to these latter vessel flights.
Thales launched the CAPTAS 4 Compact family of VDS systems at Euronaval in 2016, with the intention of maintaining the active hard body and passive array performance of the full-sized CAPTAS 4 while reducing platform SWaP impact through a major reconfiguration of onboard elements. This is achieved through the use of components from smaller CAPTAS sonars, which enables Thales to claim that while CAPTAS 4 Compact has not yet been delivered as an entire system, risk is managed through the known performance of these field-tested (albeit newly integrated) components.
CAPTAS 4 Compact is available in two variants. The Independent Tow variant simply reduces the onboard SWaP while maintaining the need for three tows in the water for full ASW functionality (including torpedo defence). The Dependent Tow variant adopts the design of the CAPTAS 2, where the passive array is manually clipped behind the active hard body at each deployment. This results on only two towed elements being deployed (including torpedo defence) but at the cost of the need for manual intervention at each deployment and recovery.
Either CAPTAS 4 Compact variant would offer both shipbuilders where CAPTAS 4 (or its UK variant) is incumbent a reduction in onboard SWaP, allowing the vessel to use the space for other purposes. For the F-5000, CAPTAS 4 Compact may offer a second option to the Ultra ISS VDS, as its reduced SWaP would somewhat reduce platform re-design impact and risk, compared to adoption of a full CAPTAS 4 system. This however would be at the cost of bi-static capability and operator interface commonality unless Ultra’s ISS integration layer remained incumbent over the entire ASW system.
Ultra’s evolved VDS configuration can be surmised from their participation in the Canadian Surface Combatant (CSC) program where, as in Australia, they are ASW supplier into both Navantia and BAE teams (though for CSC, Ultra is BAE’s sole ASW provider, unlike in Australia and the UK where it shares this role with Thales). Equally notable was the presence at Pacific 2017 of an active hard body derived from Ultra’s Low Frequency Active Passive Sonar (LFAPS), which is in service with the Royal Netherlands Navy. Ultra’s evolved VDS approach is expected to involve the introduction of an active hard-body source alongside its existing ISS active and passive array, with torpedo defence capability integrated into that array.
This approach would leverage both program and operational commonality with the Ultra ISS, as the essential configuration of capabilities, integrated processing and user interfaces would not change. In the majority of expected operational scenarios, a naval commander would be able to gain full ASW functionality from a single deployed horizontal VDS tow, incorporating torpedo defence capability. In those situations where sea-state and manoeuvre requirements permitted and where higher active source levels were desired, the separate active hard-body could be optionally deployed to provide further system performance from a second towed element. As with CAPTAS 4 Compact, while Ultra claim that risk is controlled due to all system elements being mature and fielded, this is a reconfiguration and new integration of those elements.
Conclusion
Both Thales and Ultra have significant ASW capability differentiators, and at a sensor and system component level the Commonwealth and the three shipbuilders are blessed with an abundance of choice as they move forward through the Sea 5000 Competitive Evaluation Process. However, what rapidly becomes clear from a direct comparison of reference ship ASW configurations is that they do not all provide a forward step from DDG in key elements of ASW capability.
The challenge facing the Commonwealth is not just to select a Future Frigate with the best starting ASW system. The real challenge is to choose the best roadmap for the building of a comprehensive and strategically crucial RAN ASW capability based on the selected platform, a roadmap that started with the DDG and will extend well into the next half century.
ASW Concepts 101 Mono-static: The acoustic transmit and receive path goes from, and back to, the one stand-alone sensor system (whether a HMS or VDS). This is the standard way in which sonar systems have operated, and does not include any level of integration between sensors. Bi-static: This is where a ship’s sonar sensors can operate together, as well as independently (mon-statically), so that the HMS transmits and the VDS receives. This increases the possible sonar paths available to the ship and therefore increases the likelihood and accuracy of detections. Bi-static operations require an integrated ASW processing architecture. The Hobart-Class DDG is one of the only ships in the world to have this capability. Multi-static: An extension of bi-static operations. This is where remote sensors can be used in conjunction with the ship’s ASW systems to transmit or receive, thereby building a much broader theatre ASW picture. Remote sensors may include the sonars of other vessels in the task-group, sonobuoys, autonomous vehicles (air, land or sea borne), or other capabilities. This is an exciting area of ASW capability development which again relies heavily on an integrated processing architecture. |